This article was updated Feb. 16, 2023. It was originally published Sept. 7, 2000.
RELATED: NET-SHAPE metal parts in one shot Sand Casting Iron
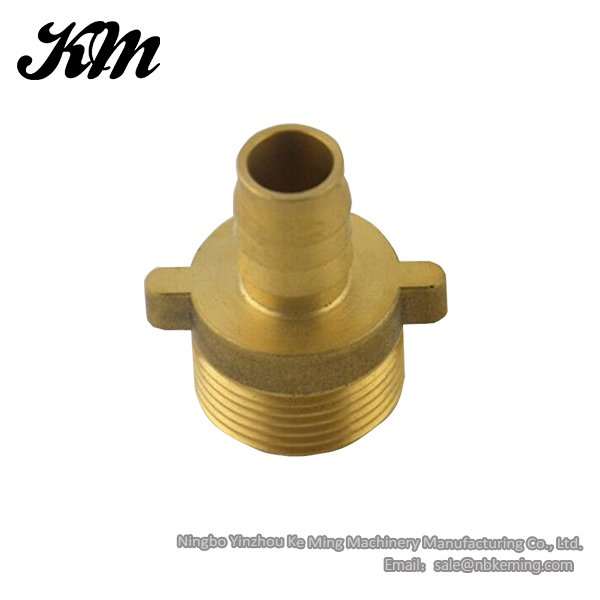
Investment casting offers several advantages over other production methods. But to make full use of the technology, designers must be aware of its limitations. Here are several tips for getting the most out of investment casting.
Investment casting can probably make a greater variety of shapes than any other manufacturing method. In many cases, shape complexity is almost not a factor in the finished part’s cost. If inserts such as ceramic cores and soluble waxes are not used, shape complexity becomes an expense only at the tool stage, and it would be a one-time cost. For investment-cast parts, features such as internal passages, through holes, concentric cylinders, and curved and tapered holes are as simple to cast as external forms such as bosses, flanges and shoulders. There is also no need to add draft angles because wax shrinks as it cools, making it easy to remove injection dies.
Part shape does, however, affect how parts solidify or “freeze.” Ideally, freezing should start the part’s extremities and then move back toward the gate where molten metal is poured into the mold. Therefore, gates should be placed in sections of the mold with the largest volumes.
Molten metal shrinks as it solidifies. How much it shrinks and how it affects the part’s shape is a function of the metal and the part’s design. For example, the longer the part dimension, the more the part will shrink in that direction. As a result, shrinking makes it hard to control dimensions in parts long in one direction and short (or thin) in the transverse direction. The dimensions of “stocky” parts are easier to control than those of long, slender parts. Therefore, it is wise to keep overall size ratios (either mass or dimensional) to less than 4:1. If needed, secondary sizing and straightening operations can repair parts that deform when solidifying.
RELATED: Precise Pressure and Flow Control Improve Wax Injection
Aspect ratios between sections of a part should also be considered. Ideally, investment castings are constructed like a carrot, with the thinnest sections farthest from the gate. Thin sections freeze first. So, if there’s a thin section between two thick sections and only one gate, the flow of molten metal will be interrupted and voids in the metal can form.
Unfortunately designing parts in a thickest-to-thinnest arrangement is not always practical. The design might call for tubes or chambers with relatively thin walls between thicker end sections, such as flanges or mounts. If so, follow similar aspect-ratio guidelines that apply to overall parts: Keep the mass or dimensional ratios between adjoining sections to 4:1 or less where possible. Avoid abrupt changes in section thicknesses. Make gradual transitions between them. If thin walls are necessary, consider adding short ribs to support the walls. Also, add fillet radii if possible and avoid sharp edges that can lead to tears and cracks as parts solidify.
There are software tools that work with CAD packages to analyze metal flow. They can help designers avoid or lessen problems with solidification. The programs predict where parts will shrink beyond design limits and let engineers adjust gates to prevent problems. This can be done before costly prototype testing.
Perhaps the only upper-size limit on investment castings is a function of how much weight can be supported by the mold. Parts weighing 150 lb or more can be cast, but it's advisable not to keep parts to 100 lb or less. On the lower end, castings usually weigh more than an ounce, and even then there are handling problems due to the small size.
Wall-thickness limits are governed by aspect ratio limitations and thick walls are easier to pour than thin ones. An absolute minimum limit of 0.030 in. is possible, but 0.094 in. (3/32) is more common. External dimensions typically stay within a 30-in. cube. Special wax injection and shell equipment may be needed for larger parts.
Combining several parts into a single unit and making it in a single forming operation saves hours of assembly and finishing. However, many designers mistakenly believe combining parts is best done with plastic parts, such as headlight nacelles and power-tool housings.
But investment casting can do the same thing with metal. Features such as tubes, bosses, fins, cams, flywheels, gear racks, handles, bowls, chambers, detents, hooks, snaps and housings can all be combined in a single unit in one operation. For example, a jet-engine maker combined 88 metal pieces into a single compressor part. And the more pieces combined, the greater the manufacturing savings.
Combining parts also eliminates much of the fastening and joining that accompanies assembly. Joining four parts—or at least their functions—in a single component does away with most of the welding, riveting, and threaded fasteners, as well as the fixturing, assembly operations, straightening and scrap. That makes sheet-metal items, stamped parts and machined parts joined by welding or mechanical processes good candidates for assembly-by-investment casting.
RELATED: Investment or Sand Casting? Which is Right for Your Application?
Here are some tips for turning several parts into one multi-functional investment-cast one:
Reconsider the parts’ functions. A fitting, tube, indexer, collar, brace and mounting bracket serve individual functions, but when assembled, they do a single task. Try replacing them with one piece that does the entire job.
Be prepared to change the shape or metal. If possible, keep the thickness of various sections constant. If not possible, make gradual transitions from one section to another. Avoid having several sections meet at one point, and stagger meeting points to avoid large mass points. Also, thin walls may need ribs or shoulders for strength. Finally, if the shape of the design is complex, perhaps an alloy can be more easily cast to get flow into all sections.
Design parts so as many as possible fit on an investment-casting tree. Visualize the part as being one of a cluster of parts on a casting tree. Casting is more efficient and less costly as the number of parts attached to a tree increases and the number of gates per part decreases. These are the critical factors in final per-unit costs for investment casting.
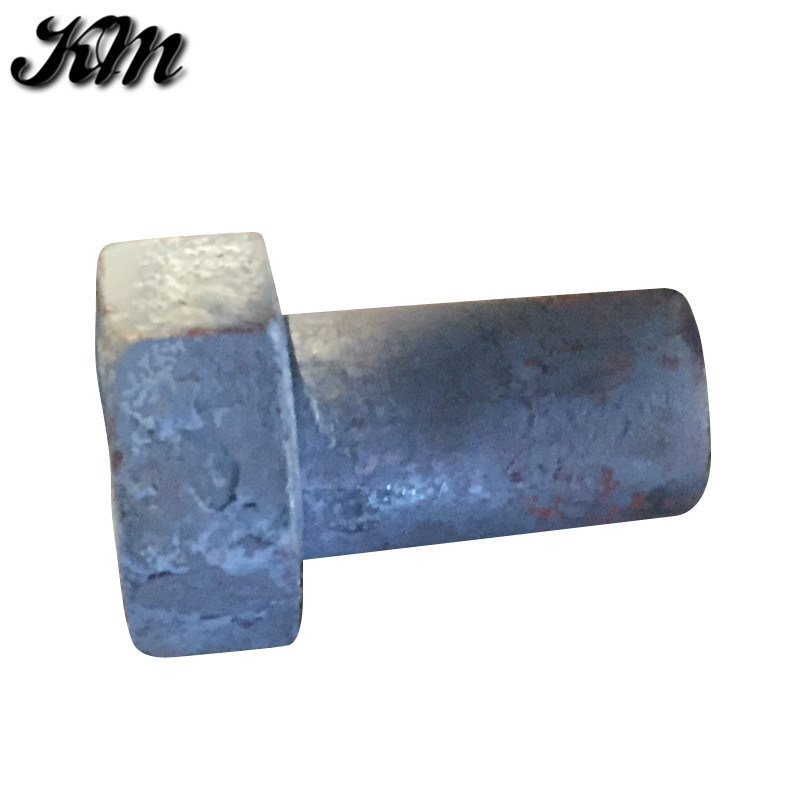
Steel Casting J. Michael Simmons was a technical director at Southern Tool when this article was originally published.